精心挑选《精益生产培训心得体会》相关文章文案。(精选5篇)
更新日期:2025-05-23 21:28
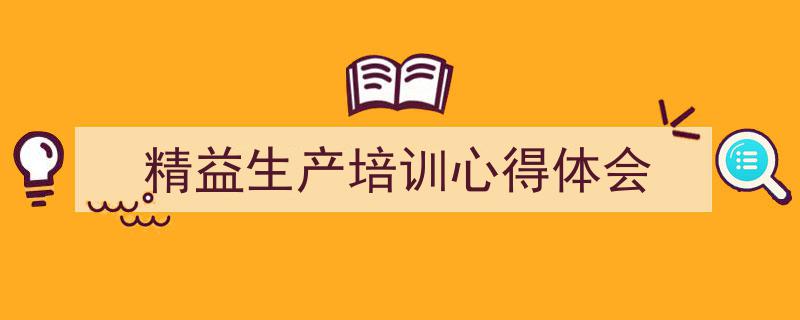
写作核心提示:
写一篇关于精益生产培训心得体会的作文,以下是一些需要注意的事项:
1. 标题明确:选择一个简洁、有吸引力的标题,能够概括文章内容,如《精益生产培训心得体会》或《从精益生产培训中收获的成长》。
2. 引言部分:简要介绍精益生产的基本概念,以及培训的背景和目的。可以提及自己对精益生产的初步认识,以及希望通过培训提高自身能力的期望。
3. 培训内容概述:详细描述培训过程中的主要内容和重点,如精益生产的理念、方法、工具等。可以结合实际案例,阐述如何将这些知识应用到实际工作中。
4. 培训收获:总结自己在培训过程中所获得的知识、技能和感悟。可以从以下几个方面进行阐述:
a. 对精益生产理念的理解:阐述培训使你对精益生产理念有了更深刻的认识,如“以客户为中心”、“持续改进”等。
b. 精益生产工具的应用:介绍培训中学到的精益生产工具,如5S、看板、价值流图等,以及如何将这些工具应用到实际工作中。
c. 团队合作与沟通:分享培训过程中团队合作与沟通的经验,以及如何提高团队协作能力。
d. 个人成长:描述培训使你在个人能力、职业素养等方面取得的进步。
5. 反思与改进:结合自身实际,反思在精益生产实施过程中遇到的问题和困难,以及如何改进。可以从以下几个方面
精益生产的心得体会分享
精益生产理论学习经验分享(最简单地:一切都是为了缩短时间,时间就是金钱)。精益生产一切从改善开始,将传统经验变成科学有效的方法,杜绝浪费,进而为企业实现更多的利润。一.对改善的认识
1.改善行为准则
这次培训班,徐老师首先给我们写了改善动作的20条规则,我个人认为对指导改善还是挺不错的,如下;(1)好的就是坏的,坏的就是好的,一定要能坚持走下去,永远走改善。(2)永无止境的追求a)增加1%以上的劳动力b)降低不良率缩短交货时间d)减少库存e)节省空间(3)有问题就要改善。没问题就别等改善了。(4)要打破一个人、一个流程的固定操作的传统观念,向一个人操作多个流程的柔性需求发展。(5)要掌握五个原则:现场、当场、当场、当场、当场、当场,而不仅仅是文字记录。(6)你可以尝试有50%的把握去做。不要等到有100%的把握去做改善。(7)改善只有尝试过才能成功,不是一次就能成功的。(8)贯彻欲速则不达的精神,马上去做。不要在会议室里思考和讨论。(9)用智慧去克服问题,而不是用金钱去解决问题。(10)走向理想的态度,不要找自己做不到的理由。(11)理想的姿势是:a) 生产 b) 生产 c) 生产回拉看板。(12)发挥团队合作精神,不要单打独斗,共同努力实现目标。(13)问五遍为什么,找出问题的真正根源。(14)顾全大局,破例为上。(15)观察是否存在固执(大木)、不理性(Muri)、不稳定(Mura)和改善为三无现象。(16)虽然改善很受欢迎,但维持它更为重要。(17)维护是指遵守标准操作。(18)具备改善循环的四种意识:a)质量意识(计划)b)维护意识(做实施)c)问题意识(检查)d)改善意识(行动处置)。(19)医生开处方,病人吃药,老师教改善,学生维护。(20)问题就是机会,改善就是赚钱。2.解决问题的两种方法
一个是创新,就是必须应用最新最好的技术或设备。这种方法必须投入大量的资金。一种是“改善”,用常识性的概念和方法,不用花多少钱就能达到改善的效果。3.改善的五颗“心”
(1)自信:相信这改善活动能给你带来收益。(2)决心:下定决心赶紧去做,不要闷闷不乐,优柔寡断。(3)耐心:永远坚持改善下去,结果自然就来了。(4)关心:表现出你对员工的关心和重视。(5)爱:鼓励或奖励来激励士气。二、组织改善活动
1.改善活动方式
改善活动的意义:在咨询师的指导下,由不同部门的成员组成的小团队,在特定的时期内,针对改善特定的主题开展工作。改善活动频率:每月一次改善天:一般3-6天。改善组的组数:2-3组。每组人数:一般3-9人。2.改善活动的程序安排
(1)初次会议(通常在会议室进行1-2小时)目的:a)回顾之前改善活动的进度;b)汇报全面改善活动的难点。c)改善小组组长汇报本期改善的主题。(涉及的报告主要有独立研究社登记表、价值流程图、操作人员分配表、标准作业表、成绩记录表、改善前后对比表)d)讲师的改善方向。e)背诵改善动作20码。(2)开展改善现场活动(3-40小时)a)所有改善团队成员和顾问教师将前往现场参加改善。b)按照改善八步开展改善活动。(八步:拟定主题、设定目标、调查现状、分析原因、尝试对策、确认效果、维护标准、规划未来改善)c)掌握五事原则(临场、临场、临场、临场、临场、临场、临场)。D) 改善要本着“太慢,来不及”的精神进行。(3)在会议室准备报告材料(最后3-4小时)需要准备的主要材料有:价值流程图、改善例题、柏拉图、五问表、成就记录表、未来计划。(4)召开末次会议(最后2小时)a)每个改善小组报告改善项目活动。(涉及表格:独立研究会登记表、价值流程图、改善 Express、柏拉图、五问表、改善案例、改善成果表、标准作业票、作业员赋值表(改善后)、未来计划)b)指导老师点评。c)公司最高管理级别评论。d)结束会议。三、改善活动的实践
1.改善的八步
(1)主题选择
使用形式:独立研究所登记表。要点:主题要根据动词+名词的描写来写,比如提高劳动力生产,缩短交货时间等等。(2)目标设定:
使用形式:独立研究所登记表。要点:为改善主题选择合适的衡量指标。利用前改善指标和改善的目标指标实现指标量化。(3)现状调查:
使用表格:时间观察表、价值流程图、操作员分配表、标准作业组合表、加工能力表、柏拉图五问表、改善结果表。要点:是现状调查,不是数据收集。现状调查就是要“找到真正的原因”,同时掌握五个在场原则。(4)追查真正的原因:
使用形式:改善 Express、五问法、运算符赋值表。要点:运用“发现真因七法”是:五显法、五询法、比较法、放大法、解剖法、地图法、潜水法。(5)试行对策:
使用形式:改善快递,改善案例重点:a)消除三不,即不讲道理,不稳定。b)慢一点,快一点,慢一点,c)用智慧解决问题,而不是用钱。d)有50分把握做改善,不要等到一百分再做改善。(6)效果确认:
使用表:每小时生产状态表,生产计划表,改善成绩表。重要:如果效果不好,重复3-5步。结果应该量化。(7)标准维护:
使用表格:标准操作票、操作员分配表、每小时生产状态表、生产计划表、操作标准书和人为错误表。要点:应加强管理工具的目视检查,一旦出现任何异常情况,应立即采取措施予以纠正。(8)未来计划:
使用形式:改善快递要点:先设立观摩学习示范线,再尝试将改善的动作推广到其他地方。2.改善成果衡量指标
(1)劳动力生产力=产出/劳动力投入(生产力=产出/投入)。(2)交货时间=库存数量/每天生产速度制造交付时间=(物料+在制品+成品)/生产每天的生产率生产交货时间= WIP/生产每天的速度(3)一次通过率= *100%(4)移动率=移动时间/生产计划时间(5)三个准确率=准确率*正点率*准确率。准确率=良品实际良品率/良品计划良品率。准时率=按订单要求完成的良品数量/计划完成数量。准序列率=序列完成项目数/生产计划序列项目数。(6)供货总合格率=质量效率*成本效率*交货效率(QCD)(7)换模时间:因产品型号变更,必须换模或生产条件必须重新安排,生产停止的时间。换模工时:换模所消耗的工时。精益管理干货分享——企业管理层实施推进精益生产管理心得体会
首先,要用正确的认识精益管理指标拉动改善,在管理中我们每个岗位、每项事都要确立管控指标,要有完善的“奖罚”鼓励机制,但要规避“奖罚”失当导致劳资关系的恶化。要遵循发现问题与改善空间、平衡领先指标结果指标、责权对等、管理完整流程、全局思考的原则来实现促进改进、评价工作的目的。
其次,识别问题才能改善问题,首先我们要创造敢于暴露问题的氛围和环境,让员工乐意反馈问题,管理及时有效解决问题,暴露问题时要先暴露自己的问题、对事不对人的原则,让所有人都看到问题才能更好解决问题。
发现制程中问题时首先要学会识别浪费,逐一梳理每个生产环节是否存在有八大浪费(超量产浪费、库存浪费、等待浪费、搬运浪费、不良浪费、加工过程、动作浪费、管理浪费),也可以通过数据找出问题,但要注意数据的准确性、及时性、详细及标杆以便问题的分析。
以下是不同岗位对于实施精益生产管理的体会:
1、善于发现问题
在对事不对人的前提下,以勇于暴露自己的问题来营造问题反馈的氛围和环境,使一线人员能够积极反馈问题,同时可以依据事情的本质通过数据来发现问题。
2、善于解决问题
首先要有敢于同问题较真的精神,具备善于总结并运用的技能。其次应该多到现场,做到现场问题,现场确认,现场解决。最后要能够发现一线人员工作智慧,听取一线人员建设性意见。
3、生产成本控制
围绕人、机、料、法、环对超量生产、库存、等待、搬运、不良,加工、动作、管理等方面的浪费,以不增加价值为核心进行合理优化
4、车间现场改善
现场改善成果如何能持久维持,主要在于正确领会现场改善的意义,深入理解,并彻底执行,才能使持久提升
5、深入企业精益改善
以工作质量改善为核心,重点表彰一线人员的优秀事迹,营造一线人员参与对“事”更深入地研究的氛围,从而让更多将更多事研究到精致,展现形式包括提案改善、管理改善,5S改善,优秀员工等
以上就是今天分享的关于企业管理层实施推进精益生产管理的心得体会,如果你对精益生产管理还有哪方面疑问,可以私信我,有问必答。
#管理##车间现场##企业管理##财经##经济#